Residential area in Strasbourg: the Sensations Program
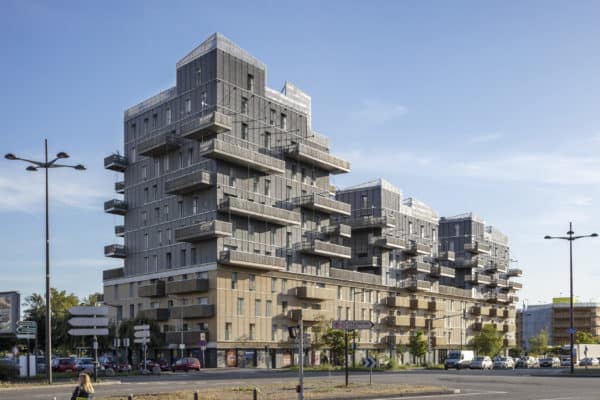
Contributor
p.michel@bouygues-immobilier.com and thalie.marx@strasbourg.eu
Description
A genuine architectural achievement for one of the first low-carbon demonstrator high-rise buildings. 11-storey building of 146 flats.
On a concrete base, the cross laminated timber (CLT) floors, including the floors, lift shafts and staircases, offer spacious accommodation that is generously open to natural light. This project is a perfect illustration of the best that wood can offer in response to the challenges of urban density.
The Sensations program by Bouygues Immobilier (lot No. 2 for home ownership) is part of a much wider project led by the Strasbourg Eurometropolis in the Two Rivers sector, in the Rhine Port district. It consists of the construction of a low-carbon wood residential block comprising 446 homes spread over 29,700m² of floor space, including a 320-space car park. The aim of this program is to experiment with the construction of a large-scale block, using wood as much as possible (particularly for the structure) with heights that are rarely achieved in France (5-10 floors), and with low energy consumption (half of the buildings are passive). This experimentation is linked to the development of a wood industry.
The programme also proposes a geothermal network shared between the different lots on the site, allowing reversible floors (hot and cold) to be created within the buildings.
- Quality of housing
- Materials
- Building
Factsheet

- Metropolis
Distinction
Media
Project evaluation*
based on contributor declaration
Criteria n°1: SUFFICIENCY
Confronted with the need for urban densification, Sensations demonstrates the relevance of laminated wood for building high buildings in a more ecological way. 3 buildings of between 8 to 11 floors accommodating 146 housing units
On a concrete base, including the floors, lift shafts and staircases, offer spacious accommodation that is generously open to natural light.. A demonstration project showcasing the possibilities of wood today and quality, bio-sourced materials, a lower carbon footprint thanks to the presence of wood, all constitute the beginnings of the best that sustainable architecture can bring to housing and to the city as a whole. FROM THE FLOORS TO THE CEILINGS, FROM THE FLOORS TO THE FACADES AND EVEN THE LIFT SHAFTS, THE OPERATION IS 100% WOOD. Only the staircases and the ground floor are made of concrete, for regulatory reasons. These features make this building a first in France. “Sensations” also sets a height record: with its 11-storey structure rising to 38 metres from its base, the building is the tallest 100% timber structure in France to date.
Epicea (northern pine) and SYLVESTER PIN (interior and exterior joinery) rock wool insulation. The wood was sourced from Austria because local production was not sufficient at the start of the project.
In total, 3,500 m³ of wood were required for the entire construction.
Again, with a view to saving resources, fine management of the altimetry was carried out in order to optimise earthworks, i.e. in order to balance the cubature of cuttings/backfill as best as possible. 51,000 m3 of excavated material was reused to reach the earthwork level and to level the green spaces.
The project achieves the Environmental regulations of 2012 BEPAS LEVEL and the BBCA LABEL, EXCELLENCE LEVEL. Use of a reversible floor to cover heating needs in winter and to ensure cooling in summer. In winter, a geothermal heat pump captures the natural energy of the Rhine water table and releases it through the underfloor heating system. In summer, the cooling system is of the “Natural Cooling” type. The false ceilings eliminate 80% of the main volatile organic compounds, the wall paints are classified A+ with low solvent emissions + recyclable floor coverings.
The building is designed according to very simple principles: highly repetitive structure, grouped fluid distribution cores, suspended balconies, this rationality will simplify the maintenance and will favour the second life of the project.
Criteria n°2: INCLUSION
A process of co-construction between the different actors of the site (4 projects) was initiated by the Eurometropolis of Strasbourg. A series of workshops between designers took place to coordinate and imagine together the cohabitation of the projects. Management of the size of the buildings, shadows, visual impacts visual impacts, urban form…
The BEPAS-level program consists of 8,451 m² SP of mixed-use housing (146 units) and 830 m² (floor area) of ground floor shops.
The wooden residential block in the Rhin port district, in the Deux Rives sector, is the signal for this reconquest. “Sensations” is the first of four lots which, on a 2-hectare site belonging to the local authority, will total 443 housing units (331 for home ownership, 112 social housing units), activities and shops, and a silo car park.
Criteria n°3: RESILIENCE
The project addresses the issue of resilience to the effects of climate change. Indeed, Sensations is based on a laminated wood post and beam structure, with facades, stairwells, lift shafts and floors made of cross-laminated timber (CLT) panels. This construction principle allows the building to be energy passive. With heating requirements that will not exceed 15 kWh/habitable m² /annum. Moreover, as the block is located in a seismic zone, the wooden structure also ensures the stability of the building in the event of an earthquake.
Criteria n°4 : CREATIVITY
The project can be seen as a “stimulus” for local businesses. Introduction of new manufacturing and design processes. This is notably the case of the prefabrication revolution
which vastly modifies conventional methods. The capacity of the project to generate new uses will be measured when the block is finalised. Our project is part of a global approach that will lead to the emergence of new uses.
In the framework of the City of Tomorrow assessment, the overall level of innovation is level 1, which corresponds to national firsts. Technical and technological innovations are level 1
The innovations targeted are multiple:
- Technical and energetic: height, compatibility between wood structures, summer comfort, acoustics, fire safety, seismic and environmental quality of collective buildings, low carbon balance;
- Construction innovation: the project proposes a very ambitious constructional system for a building of more than 10 floors, proposing increasingly light structures according to the levels of the floors. Consequently, both the foundations and ground floors are made from reinforced concrete in order to ensure that the loads are taken up, then the load-bearing walls and facades are made of laminated wood panels. Finally, the facades of the last levels and the interplot buildings are made of timber frames. A glued laminated wood post and beam system and glued wood panel floors complete the technical system.
- Collaborative project set-up with a “horizontal” consultation system with the designation, from the project outset, of a team comprising a developer to whom the lot is assigned, its main technical service providers, including companies (architect, design offices, particularly in wood engineering, and wood construction companies). This allows for a balanced exchange of ideas between the players in order to define and verify together the possible constructive solutions and the technological obstacles to be overcome;
Project team support:
– on the one hand to guarantee the level of ambition of the project by a scientific committee called the quality circle, made up of experts in the wood construction and energy performance sector coordinated by the Fibres Energivie competitiveness cluster;
– and secondly, to guarantee the operationality of the project: through a project management assistance mission to evaluate the innovation and insurability of the wood block’s constructions. The aim is to identify the subjects of innovation within the construction processes with the aim of removing legal, technical and economic obstacles, but also to establish a strategy of action to remove potential blockages and to support the obtaining of insurance for the project owners concerned.
Last criteria: potential of replicability ?
The EcoCité low-carbon residential wood demonstration block project has three objectives:
– To study the bioclimatic relevance of the use of wood in construction with BEPAS type performance levels;
– To analyse the technical and structural constraints linked to the development of wood as a major material in construction and to achieve a mass effect;
– To participate in the development of a local wood construction sector “from the tree to the building site and to the resident”.
The project can be reproduced on the territory of the Strasbourg Eurometropolis (whose objective is the construction of 300 to 400 wooden housing units per year), the wooden island is also a precursor for future infrastructure to be developed for the 2024 Olympic villages, which will also be entirely made of wood and BBCA.
The Strasbourg metropolis is participating in Lab2051 “Massifying wood construction”, which aims to study the conditions for wider deployment of projects of this type across France. Three high-rise wooden buildings have already been built in this district as part of the PIA Cities of Tomorrow.